Welcome to the World of Quality Control
Why Quality Matters:
Imagine you’re building a reputation for delivering top-notch products. Quality control ensures every item meets the standards that keep your customers happy and your business thriving.
How We Help:
Think of us as your partners in maintaining excellence. We check every details so you can be confident in the quality of your products.
Why this Guide:
This guide aims at explaining how Quality Control works, how we can help you achieve the best and make sure you can source the best quality products from your suppliers in Asia.
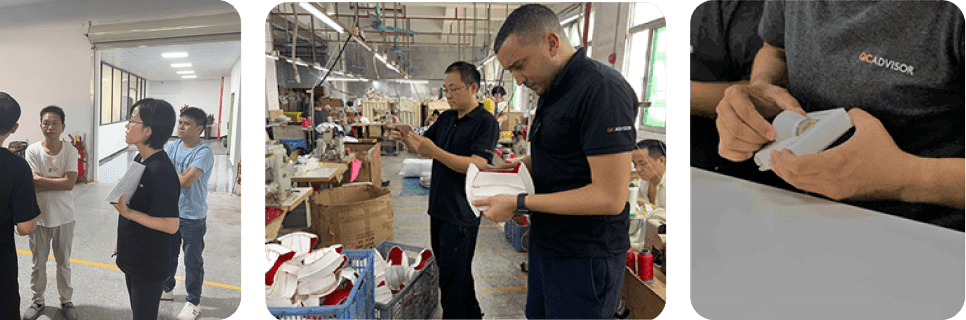
95%
of customers recommend QCADVISOR
Types of Inspections & Audits
Product Inspections:
- Pre-Production Qualification:
Ensuring all materials and processes are ready before production begins.
- Production Monitoring:
Ongoing oversight during the production process to catch any issues early.
- During Production Inspection:
Mid-production checks to ensure consistency and quality.
- Container Loading Inspection:
Verification that products are packed securely and correctly for shipment.
- Pre-Shipment Inspection:
A final check to ensure products meet your specifications before they are shipped.
Supplier Audits:
- Factory Verification Audit:
Confirming that your supplier’s facility meets your required standards.
- Factory Technical Audit:
Detailed assessment of a supplier’s technical capabilities and processes.
- Corporate Social Compliance Audit:
Ensuring that your supplier adheres to ethical and social standards.
- Customized Audit:
Tailored audits to meet specific needs and criteria for your business.
How We Arrange an Inspection at QCADVISOR
- You Book your Inspection:
You create a project and book your inspection on our platform at least 48-72h before the planned date.
The more detailed information and specifications you provide, the more effectively we can inspect your products. We also recommend preparing approval samples at the factory, so our inspector can accurately assess subjective aspects like color and surface quality.
- Quotation Confirmation:
As soon as you have booked your inspection or audit, our team will review your order details and get back to you with a quotation for your approval.
- Supplier Confirmation:
Your supplier can confirm the inspection date and location either directly through our system or simply by replying to the automated email they receive when you book the service.
Your supplier must confirm the inspection date and location to ensure accuracy and provide final factory contact details. They must notify us of any postponements at least 24 hours in advance to avoid late fees.
- Service Preparation:
Once the service is confirmed (quotation agreed and supplier confirms the inspection details), our team will prepare the inspection checklist and assign the most suitable inspector based on product expertise and location.
- Performing the Inspection:
Our inspector will conduct the inspection according to the agreed scope and quotation. If any issues arise, we’ll inform you, though we typically handle problems on our own when ever possible.
- Sending your Inspection Report:
When the inspection is completed, you should expect to receive your report a couple hours after the inspection is finished.
How to Read the Report?
During the Inspection we focus on 3 important things:
QUALITY:
This is the core of the inspection, where we examine all selected products using general industry criteria and yours specific requirements, if provided. We focus on cosmetic issues, workmanship, and basic functions (e.g., turning switches on/off, opening/closing buttons).
CONFORMITY:
We select 1 to 5 samples per SKU to verify they meet your specifications. This includes checking packaging, shipping marks, product appearance, labeling, barcodes, and dimensions.
TESTS:
Our team identifies the relevant performance and safety tests for your products, such as Carton Drop Test, Abuse Test, Running Test, and Assembly Test. These tests are customizable based on your needs.
How to Read your Inspection Results:
QUALITY:
For this part, we typically use AQL (Acceptance Quality Limits) to determine if the product passes (OK) or fails (NOK). The result might also be “Remarks” or “Pending” if there are additional remarks or/and we can’t perform the inspection as per AQL standards.
Defects are classified into three categories:
Minor
Deviation from the standard that likely won’t affect sales.
Major
Deviation that could affect sales or customer satisfaction.
Critical
Defects that may pose safety risks or fail to meet your local regulations.
CONFORMITY & TESTS:
OK
Fully complies with your specifications or standards.
NOK
Does not comply with your specifications or standards.
Remarks/Pending
Requires your review and
direct coordination with the factory as we cannot provide a final judgment.
For Reference
Information provided for your reference only, such as shipping mark photos when no specifications were given, so we cannot determine compliance.
Understanding AQL (Acceptance Quality Limits)
AQL, or Acceptance Quality Limits, is a critical tool in quality control that determines the maximum number of defects allowed in a batch of products before the batch is considered unacceptable. The process involves two main steps:
1. Defining the Sample Size
First, you determine the number of units to be inspected from the entire batch. This is based on the batch size and the desired inspection level. The sample size is selected to represent the entire shipment, providing a reliable assessment without checking every single unit.
AQL ensures that while some minor defects may be tolerated, critical and excessive issues are caught, maintaining product quality without unnecessarily rejecting entire batches.
2. Evaluating the Results
After inspection, the defects found are categorized (e.g.,minor,major, critical). Each category has a predetermined AQL threshold, which specifies how many defects are acceptable. If the number of defects within each category falls below the threshold, the shipment passes. If it exceeds the threshold, the shipment fails, indicating that corrective actions are needed.
What is a Man Day?
Definition:
A “Man Day” is a unit of measurement representing one full day of work dedicated to checking the quality of your products.
Think of it like hiring a consultant who charges by the hour. Instead of hours, we calculate our work in days. When you book an inspection, we’ll tell you how many Man Days are needed to complete the job, just like a consultant would estimate the hours needed for a project.
What’s Included:
The price for a Man Day is all-inclusive. This means it covers everything—our services, the preparation work we do before the inspection (such as coordinating with your supplier and confirming the inspection date), and the inspection itself.
Organizing the Work:
If your inspection requires more than 1 Man Day (for example, 2 Man Days), we can either:
- Assign 1 inspector to work over 2 days, or
- Assign 2 inspectors to complete the job in 1 day.
This flexibility allows us to meet your needs, especially if the order is urgent or requires special arrangements.
Typical Inspections:
For most inspections, 1 Man Day is usually enough, unless you have a large number of SKUs to inspect or a high sample size. In those cases, we might recommend more time to ensure a thorough check.
What to do AFTER an Inspection
After the inspection, there are key steps you should take to ensure your products meet your standards and are ready for market:
Understanding the Results:
We provide a detailed report of the inspection findings, helping you interpret what the results mean for your business. This includes understanding the types and severity of any defects found, and how they might impact product quality, safety, or customer satisfaction.
Talking to Your Supplier:
Effective communication with your supplier is crucial at this stage. You are responsible to discuss the inspection results, ensuring your supplier understands the issues and the necessary steps to address them. This dialogue helps prevent future issues and fosters a collaborative relationship.
Deciding What to Do Next:
Based on the inspection outcomes,you’ll need to decide on the next steps. This could involve approving the shipment if everything meets your standards, requesting rework to correct defects, or scheduling a re-inspection to verify the improvements.We’ll advise you on the best course of action to protect your business interests and maintain quality when necessary.
Quality Control Done Right: Essential Practices
Conduct a Factory Audit Before Production:
Ensure the factory has the necessary capabilities and certifications to meet your quality requirements before placing an order.
Specify Tolerances in Product Specifications:
Define acceptable ranges for measurements, weight, and other critical attributes to avoid misunderstandings during inspection.
Establish a Quality Agreement:
Create a formal quality agreement with your supplier that outlines quality expectations, inspection criteria, and consequences for non-compliance.
Use Third-Party Inspection Services:
Hire an independent inspection company to provide an unbiased assessment of product quality, particularly for high-value orders.
Set Up a Quality Control Checklist:
Develop a detailed QC checklist tailored to your product, ensuring that inspectors focus on the most critical aspects during inspections.
Monitor Production with On-Site Visits:
Regularly visit the factory during production to monitor progress, address issues in real-time, and build rapport with the supplier.
Implement a Pilot Production Run:
Before full-scale production, run a small batch to test processes and identify any potential quality issues.
Train Your Supplier on Your Standards:
Invest time in educating your supplier on your specific quality standards, especially if they are different from the industry norm.
Request Material Certifications:
Ask your supplier to provide material certifications or test reports to verify that the materials used meet your specifications.
Plan for Contingency Stock:
Maintain a buffer stock of critical products to mitigate the impact of any potential quality issues or delays.
Establish Clear Rejection Criteria:
Clearly define what constitutes a rejectable defect, so there’s no ambiguity during the inspection process.
Create a Feedback Loop with Your Supplier:
After each inspection, provide feedback to your supplier on what went well and areas for improvement, fostering continuous quality improvement.
Conduct Regular Supplier Performance Reviews:
Periodically review your supplier’s performance based on quality metrics, on-time delivery, and communication, and use this data to make informed decisions.
Use Pre-Production Samples for Final Approval:
Before starting mass production, approve pre-production samples that closely resemble the final product to minimize quality risks.
Establish Escalation Protocols:
Define clear escalation procedures for addressing significant quality issues, ensuring that they are resolved quickly and effectively.
Stay Updated on Regulatory Changes:
Keep informed about changes in international and local regulations that may impact product quality and compliance, ensuring your products meet all legal requirements.
Test Packaging for Durability:
Conduct packaging tests, such as drop tests and compression tests, to ensure that products will arrive intact after shipping.
Contact us
The quickest and most efficient way to reach us is via email. For bookings you can make them directly on the QCADVISOR platform.
If your message concerns a specific order, please reply to the booking email with the order number in the subject line. This helps us track your request and respond swiftly.
Book an Inspection/Audit:
Book directly on your account
Inspection/Audit Arrangements:
For inquiries about scheduling, date changes, address updates, multi-location inspections, or special arrangements
Technical or General Order Questions:
Reply to the booking email
Invoices and Payments:
For any questions related to billing or payments
QCADVISOR team is built from a foundation of trust, experience and integrity.
We are an international team of Quality Control experts. Our main base is China, the world’s manufacturing powerhouse.
We verify your suppliers and inspect your products in Asia, using a unique pro-active approach combined with technology. We not only catch defects, we help avoid them before they happen.
Our team has helped to build and execute Quality Control and Supplier Qualification programs for international brands and retailers such as MGB, Amazon, Ikea, Wayfair and Inditex.
We have our own style. We treat every of your project specially so we can anticipate and fulfill your requirements and needs. We are passionate people, that love what we do.
We are solely focused on Quality Control and do not engage in sourcing or other activities to avoid conflict of interest and to preserve our integrity.